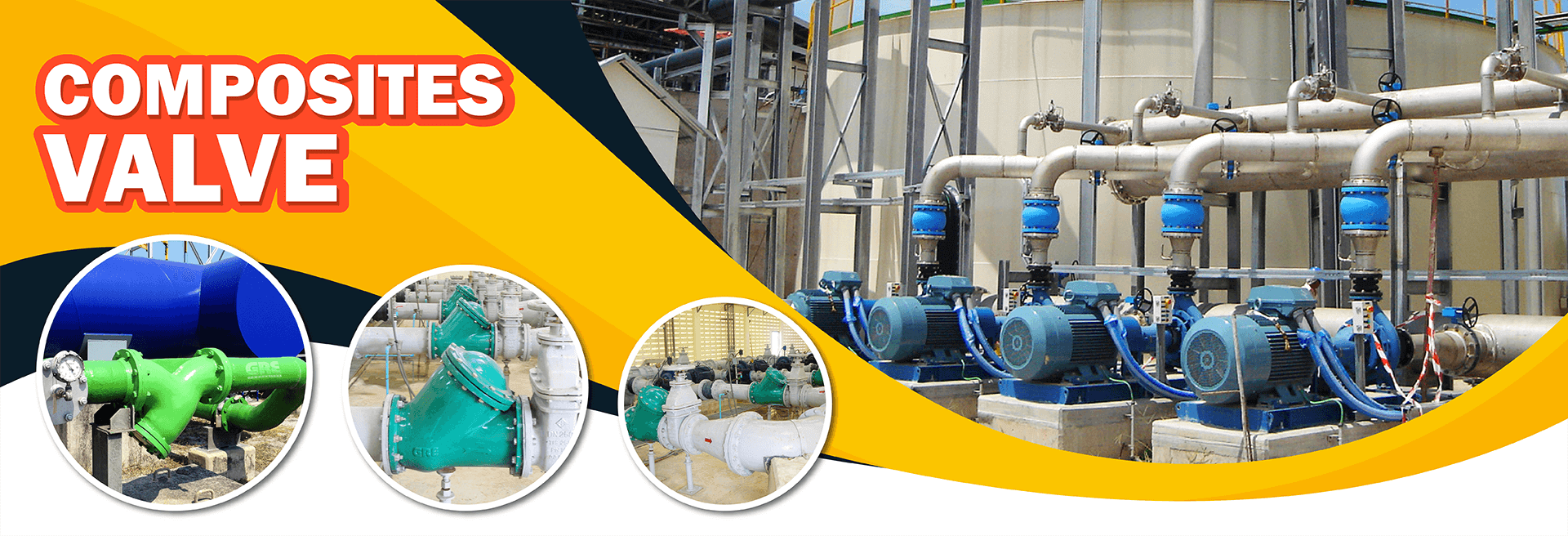
GRE COMPOSITES VALVE
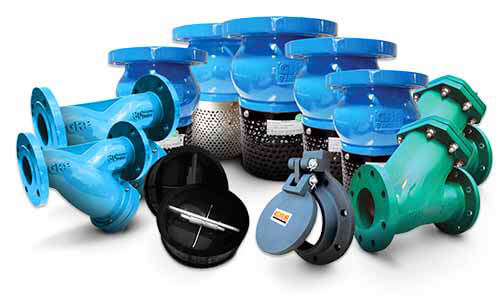
DESIGN FEATURES
OF GRE COMPOSITES VALVE
- Composites material provides excellent corrosion resistance.
- Light weight composites disc provides lower headloss.
- Light weight construction provides easy installation, especially in large size.
- Synthetic rubber seal ring provides tight sealing capability.
- Unique Inclined seat design reduces debris on valve’s seat.
- Screen and fasteners are AISI 304 stainless steel as standard and SUS316 is available upon request.
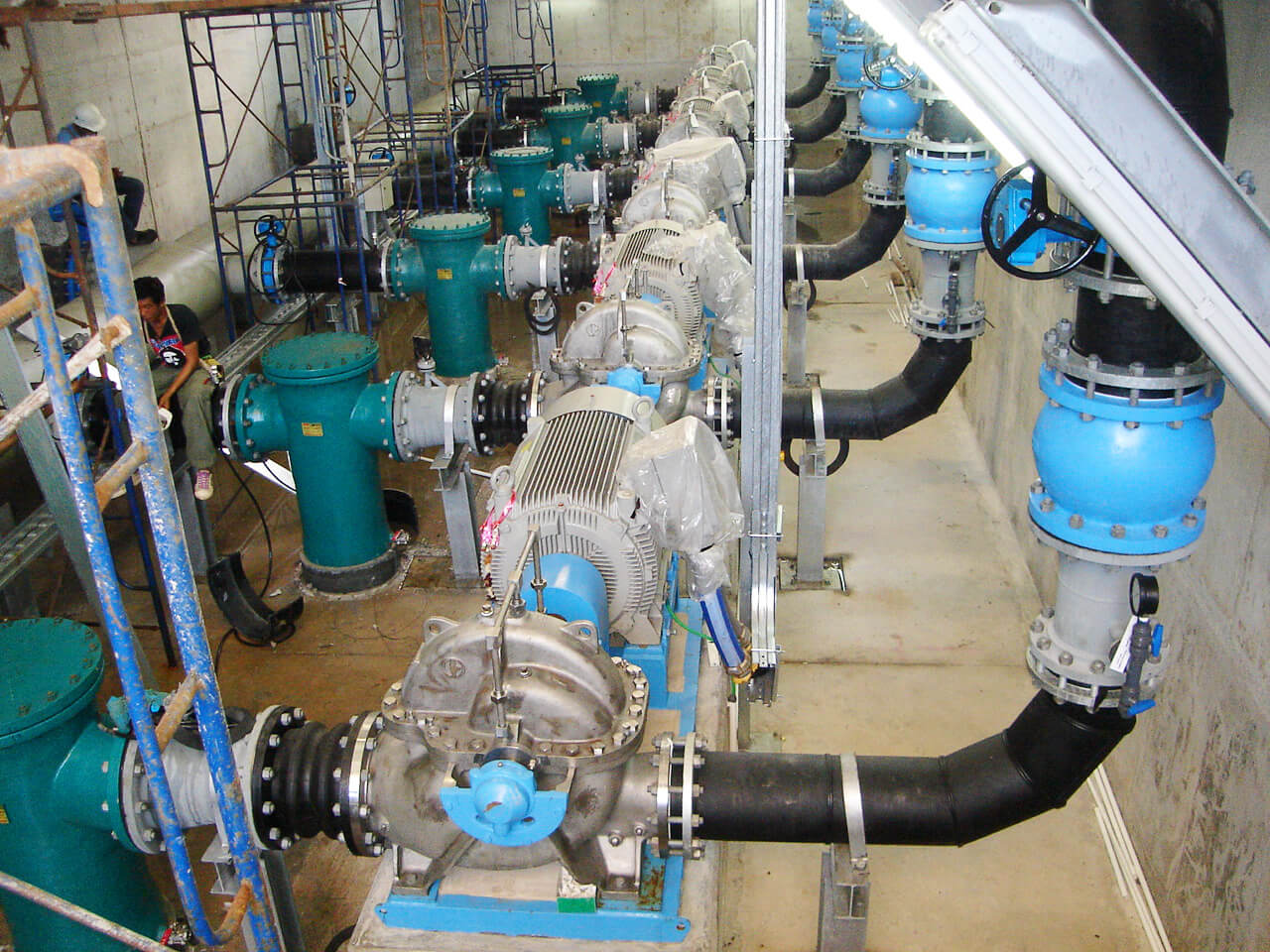
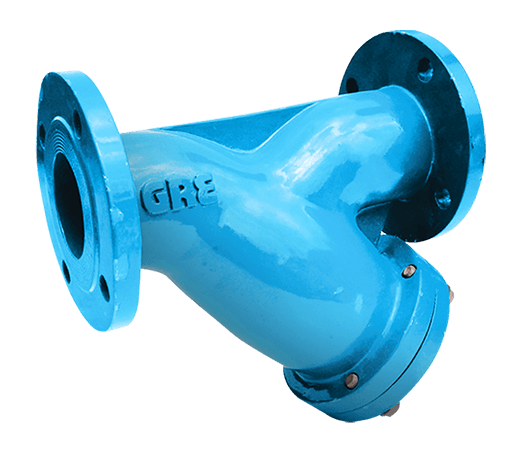
DESIGN ADVANTAGES
OF GRE COMPOSITES VALVE
- Excellent corrosion resistant
- Light weight
- Rugged construction
- Easy inline maintenance
BENEFIT
OF GRE COMPOSITES VALVE
- Composites material provides excellent corrosion resistance.
- Light weight composites disc provides lower headloss.
- Light weight construction provides easy installation, especially in large size.
- Synthetic rubber seal ring provides tight sealing capability.
- Unique Inclined seat design reduces debris on valve’s seat.
- Screen and fasteners are AISI 304 stainless steel as standard and SUS316 is available upon request.
FOOT VALVES
DESCRIPTION
GRE composites foot valves are installed on the pump suction to prevent the pump column from draining upon pump shut down. The valve has a long back axial guide for reduced displacement with a synthetic rubber seal ring providing a drip-tight seal. Unique inclined seat design reduces accumulation of debris on the seat area. The globe type-full port body design plus light weight composites disc offer lower headloss and power consumption for the system. The main parts are made from composites material, spring and bolting are made from stainless steel, making GRE composites foot valve an excellent corrosion resistant pipeline equipment for water services.
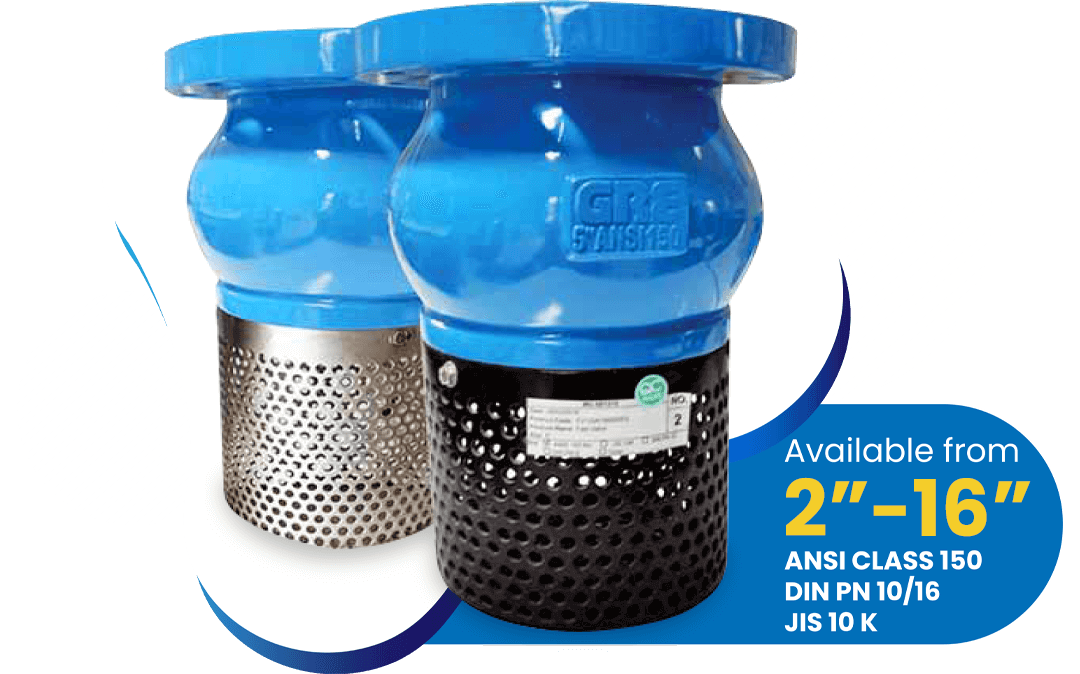
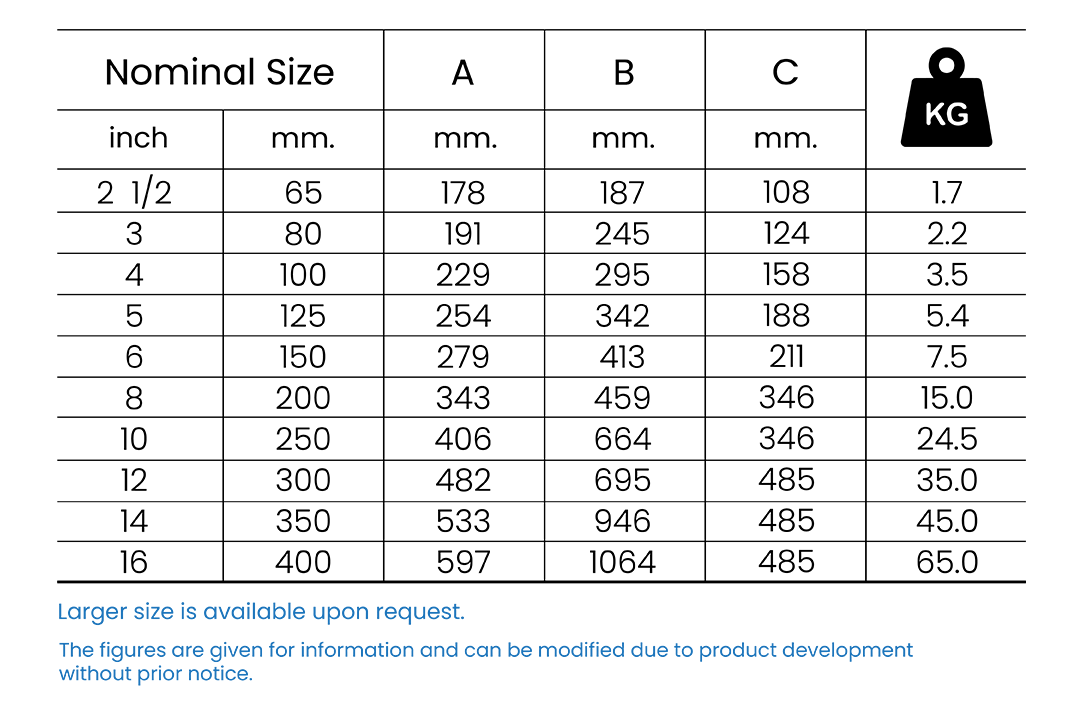
DIMENSIONS AND WEIGHTS
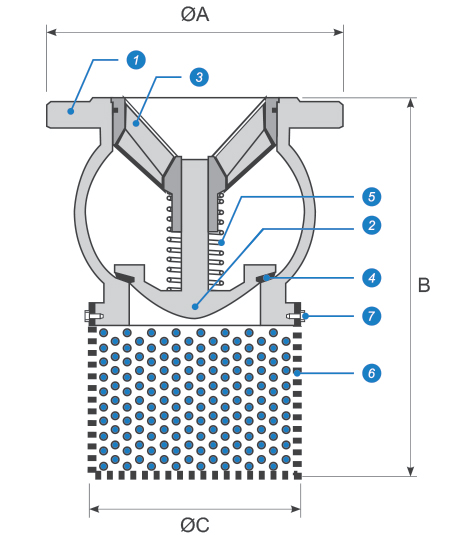
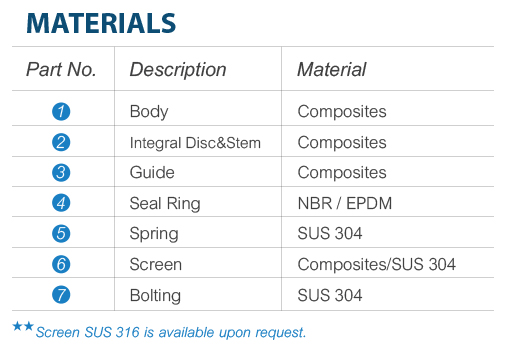
SPECIFICATIONS
-
Flange with raised face, drilled according to
ANSI 125/150, DIN PN10 or JIS 10K flanges - Maximum working pressure : 10 Bar
- Maximum working temperature : 80º C
- Maximum intermittent temperature : 90º C
- Inspection and testing per GRE standard :-
-
100% sealing tested with water at full body water column (5 psi)
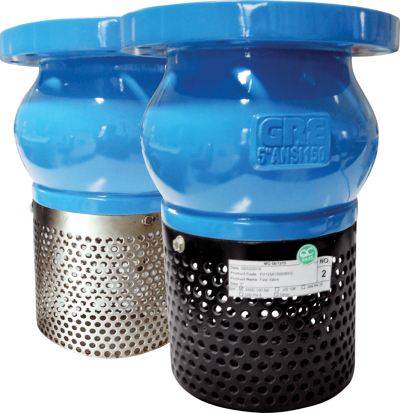
Y-TYPE STRAINER
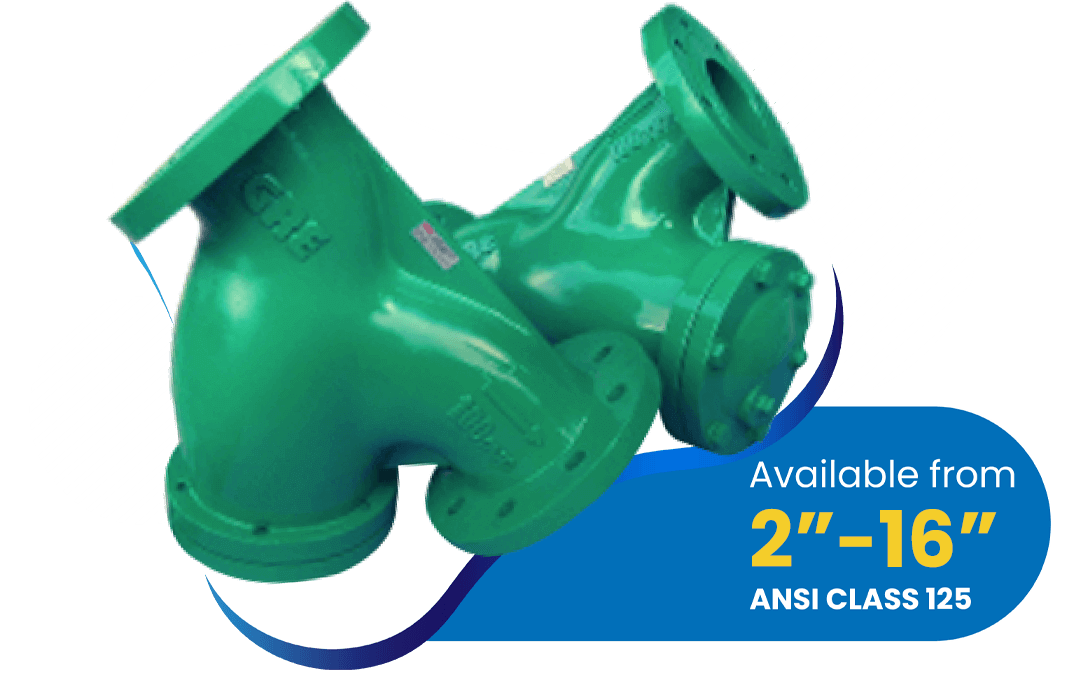
DESCRIPTION
GRE composites Y-strainers are used in a wide variety of liquid straining applications in order to protect downstream pipeline equipment, that could be damaged or clogged by foreign matters, providing very cost effective solutions for costly pumping systems. The body and cover are made from composites material. Screen is made from stainless steel, making GRE composites Y-strainer an excellent corrosion resistant straining equipment for water services. Light weight construction also is perfectly used in plastic or GRE or GRVE piping systems.
DIMENSIONS AND WEIGHTS
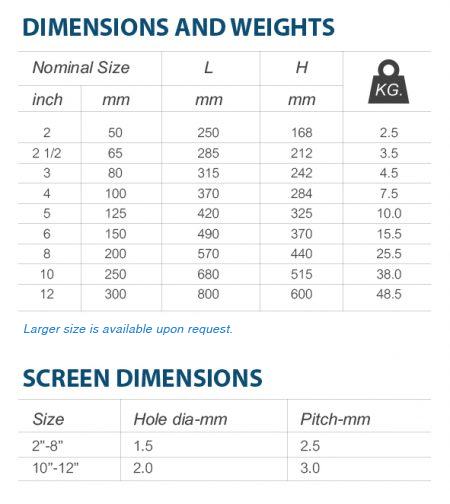
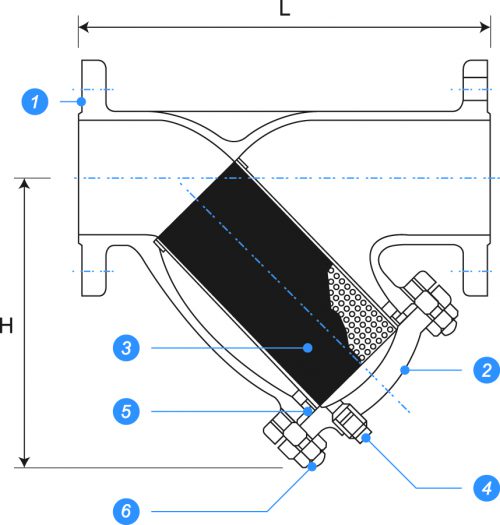
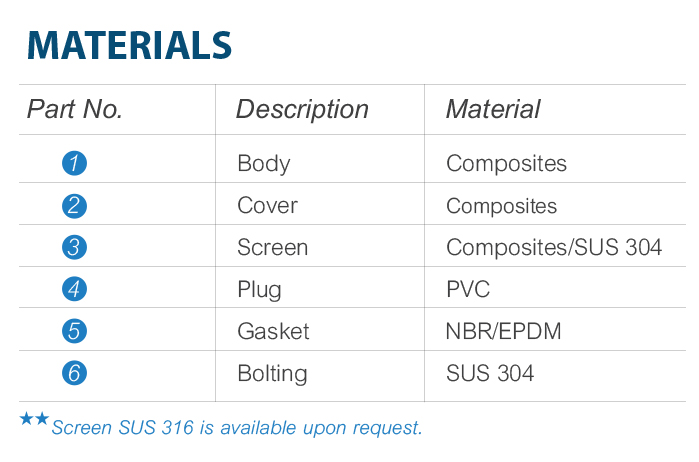
SPECIFICATIONS
- Face-to-face length according to GRE standard.
-
Flanges with flat face, drilled according to
ANSI 125/150, DIN PN10 or JIS 10K. - Maximum working pressure 10 Bar.
- Maximum working temperature 80º C.
- Maximum intermittent temperature 90º C.
- Inspection and testing per GRE standard.
-
100% hydrostatically shell tested at maximum working pressure.
- Off-centered blow down plug ensures mostly complete drainage.
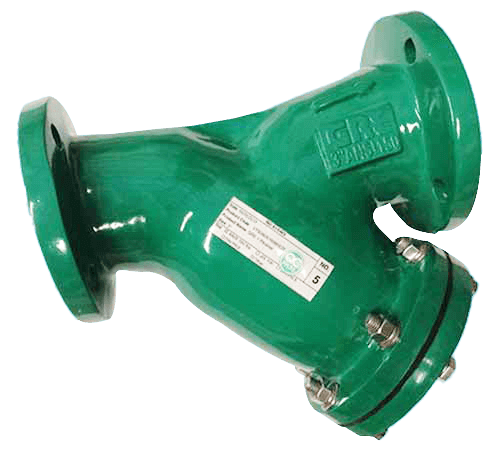
BALL CHECK VALVE
For wastewater pumping systems
DESCRIPTION
GRE composites ball check valves are specially designed for preventing reverse flow of liquid in pumping systems. These valves can be used for most of storm water, sewage, domestic and industrial wastewater, loaded or viscous liquid. Because of the self cleaning property of the freely moving ball in the valve housing, clogging problems are eliminated. The body and cover are made from composites material. The ball is lined by synthetic rubber or flexible polymer which make GRE composites ball check valve an ideal non return valve for chemically contaminated liquid likes sewage or waste water pumping systems. Light weight construction also make GRE valve perfectly be used in plastic or GRE or GRVE piping systems.
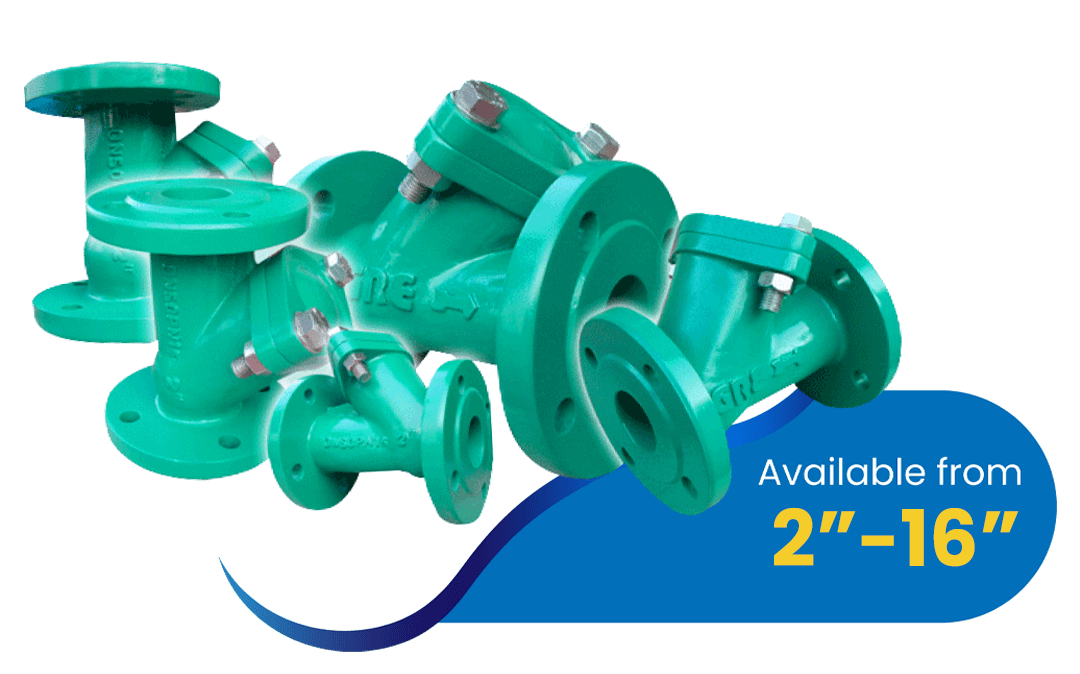
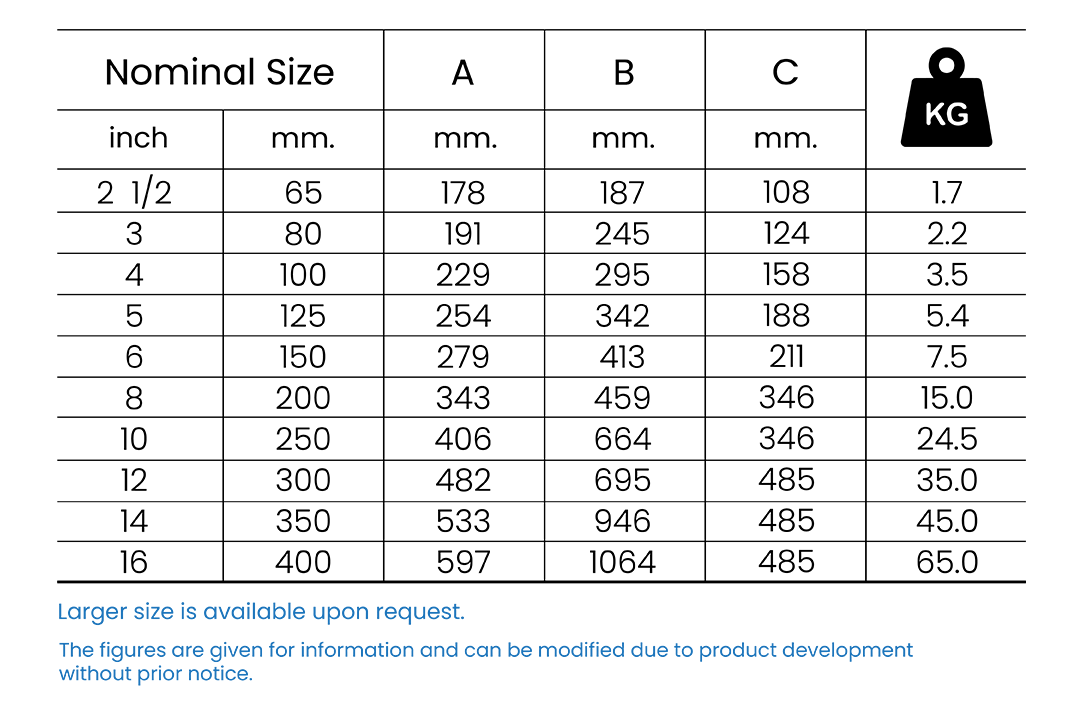
DIMENSIONS AND WEIGHTS
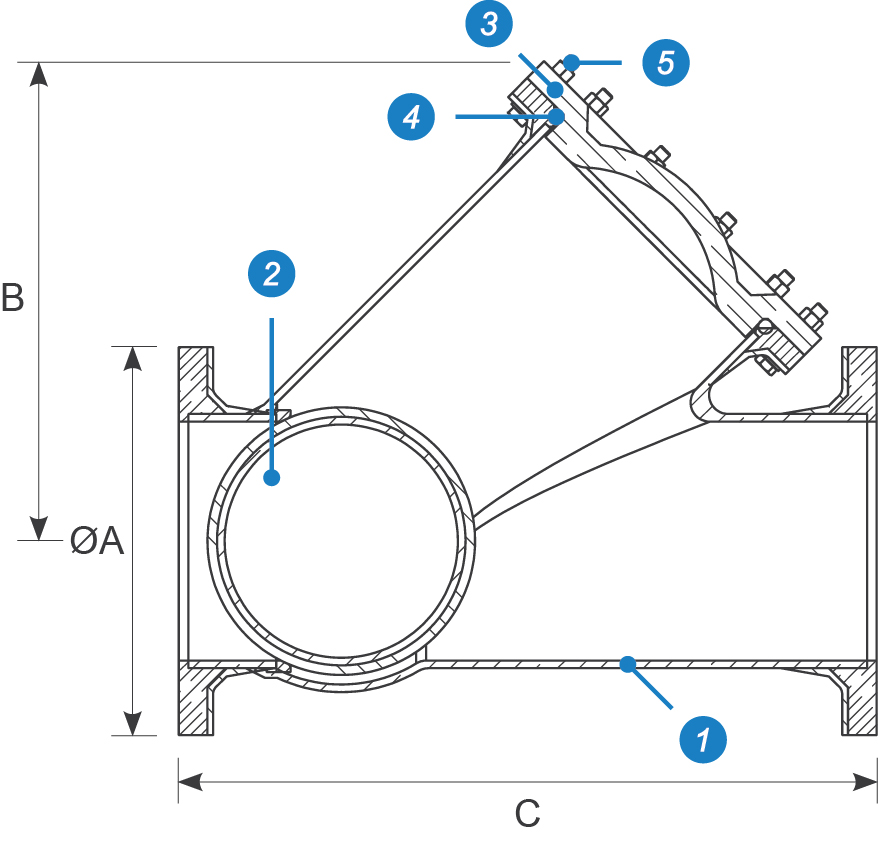
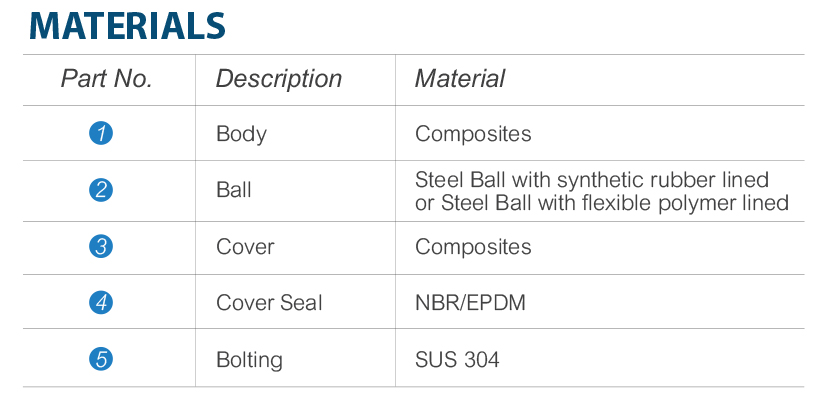
SPECIFICATIONS
-
Face-to-face length :
2”-4” : DIN3020 F6 (EN-558-1)
5”-6” : GRE standard
8”-16” : TIS 383-2524 (Long Pattern) -
Flanges with plain face, drilled according to
ANSI 150, DIN PN10/16 or JIS 10K -
Maximum working pressure :
2”-10” : 6.0 bar
12”&14” : 4.5 bar
16” : 3.0 bar - Maximum working temperature : 60º C.
- Maximum intermittent temperature : 90º C.
- Inspection and testing per GRE standard :
-
Testing :
* 100% hydrostatically shell tested at maximum working pressure.
* 100% sealing tested with water at 0.5 and 5 meters water column.
(valve in vertical and horizontal positions respectively) - Full bore design provides high flow capacity and low head loss.
- Reliable, low maintenance cost.
- Removable cover permitting easy access for inspection without removal from the pipeline.
- Can be installed both horizontal and vertical ascending positions.
WAFER CHECK VALVE
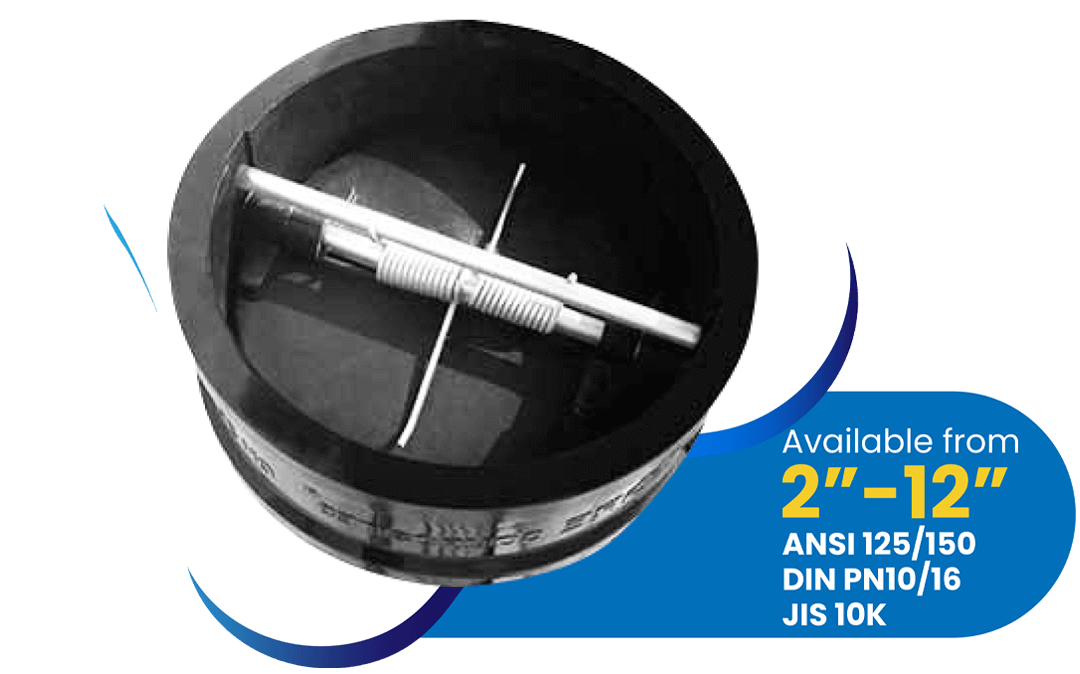
DESCRIPTION
GRE composites wafer check valves are used to prevent reverse flow of fluid in piping systems. The compact wafer style one-piece body design with dual plate save installation space and provide quiet operation when <br>compared to other conventional non return valves. An extremely light weight composites plate requires lower cracking pressure. The main parts are made from composites material, the metallic parts are made from stainless steel, making the GRE composites wafer check valve an excellent corrosion resistant pipeline equipment for water services. Light weight construction can also be perfectly used in plastic or GRE or GRVE piping systems.
DIMENSIONS AND WEIGHTS
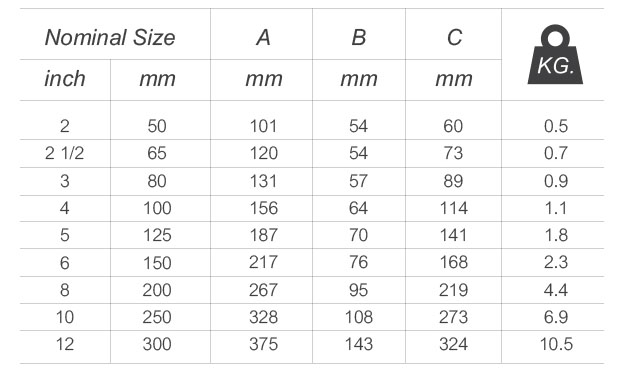
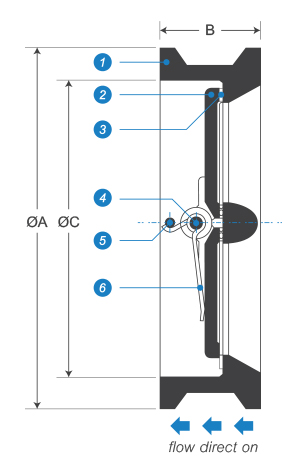
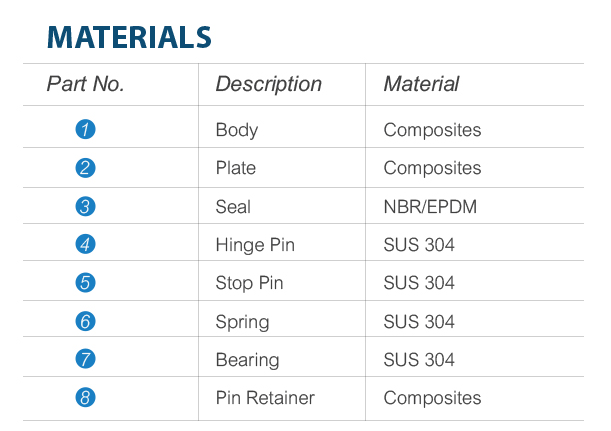
SPECIFICATIONS
- Wafer pattern with plain face.
-
For installation between
ANSI 125/150, DIN PN10/16 or JIS 10K flanges - Maximum working pressure : 200 psi.
- Maximum working temperature : 60º C.
- Maximum intermittent temperature : 90º C.
-
Inspection and testing per GRE standard :
* 100% hydrostatically shell tested at maximum working pressure.
* 100% sealing tested with water at 10 bar.
- Extremely light weight, 5% the weight of conventional swing check valves and 25% the weight of metallic wafer check valves, simplifies installation work, reduces pipe supports.
- Light weight composites plate requires lower cracking pressure & provides lower head loss.
- Light weight composites plate reduces slamming and water hammer.
- 85 degree opening of the plate ensures positive closing.
Custom-made composites valve
GRE COMPOSITES SILENT CHECK VALVE
SPECIALLY DESIGNED FOR SEA WATER SERVICE
FLANGED END – AXIAL GUIDED DISC – INCLINED SEAT
Why GRE Composites silent check valve must be selected for sea water service
– Special grade resin is carefully selected for composites material
– Inclined seat greatly reduces debris accumulated on the seat
– Light weight
– AISI 304 + epoxy coated spring ensures sea water resistance
Working Pressure : 200 psi
Test Pressure : 300 psi
Max. Working Temp : 80 C
GRE MOLDED COMPOSITES WALL MOUNTING FLAP GATE SERIES MCR-DR
DESIGN FEATURES
– Rigid composites frame, manufactured from compression molding process.
– Double hinged joint for better seating and optimum sealing capability.
– Durable & light weight flap: Made from engineered composites material, customized for any specific density. Can be opened under low unseating head.
– Lifting eye to allow manual opening of the flap in order to flush out any debris.
– Integrally casted flexible polymer onto the flap’s edge. No matallic retainer bar or bolting id used – No corrosine part.
FLAP GATE
How to Specify GRE Composites Double Hinge Flap Gate
The following Information is required to prepare quotations and typical drawing.
– Type of liquid: Water, Sea water or Sewage, etc.
– Primary Function: Pump discharge, gravity flow or tidal with wave action, etc.
– Size f opening or pipe size.
– Maximum seating head.
– Type of mounting: Wall mounting/ Pipe flange mounting.
BASKET STRAINER
FIRST INTRODUCED IN 2021
DESIGN SPECIFICATION
– Face-to-Face length according to GRE Standard.
– Flange type full face, drilled according to ANSI, DIN, JIS or Customer recuest.
– Design pressure: 150 psi(10 Bar)
– Maximum working pressure: 150 psi(10 Bar)
– Maximum working temperature: 60c
– Inspection and testing per GRE Standard
(100% Hydrostatically shell tested at 1.5 times of design pressure)